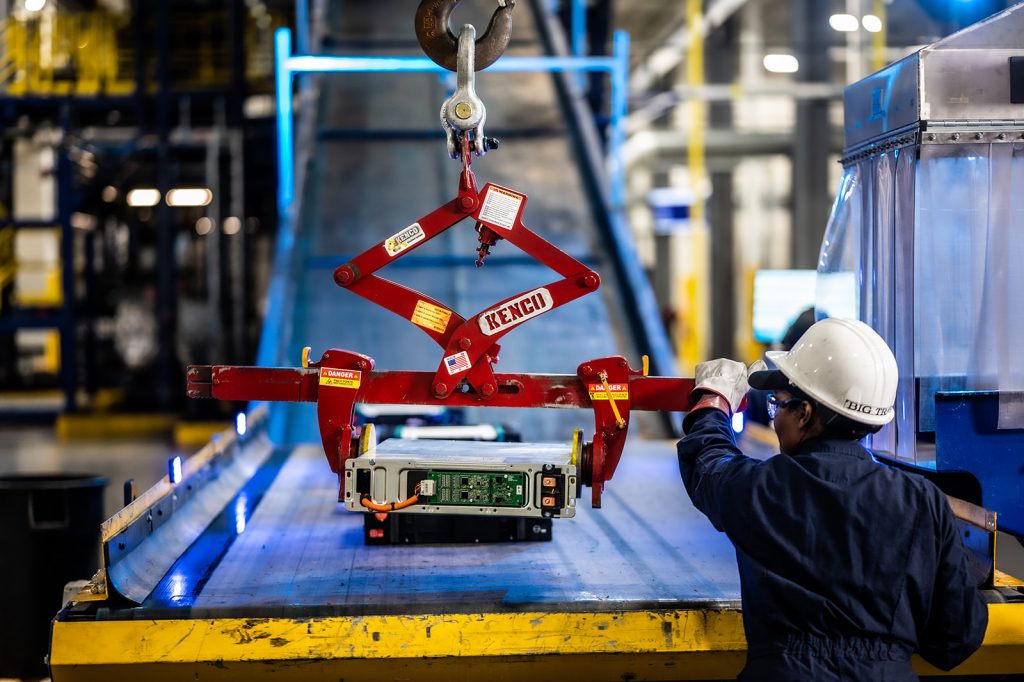
The electric vehicle (EV) revolution is driving an unprecedented surge in demand for lithium-ion batteries. But what happens to these batteries when they reach the end of their life cycle? Li-Cycle, a leading battery recycling company, is tackling this challenge head-on with innovative technology that recovers critical materials from spent batteries.
MiningFeeds recently spoke with Li-Cycle to discuss their unique approach to battery recycling, the future of mining technology, and the critical role of battery materials in a sustainable energy future.
Li-Cycle emphasizes the recovery of critical materials from lithium-ion batteries. Can you explain how your Spoke & Hub Technologies™ enable this process?
Li-Cycle’s two-step Spoke & Hub business model enables us to safely receive and recycle lithium-ion batteries regardless of condition, form factor, and state-of-charge. Our proprietary technology helps create a localized, secondary source of battery materials through ‘urban mining’ – a process that sees us reclaim critical minerals from spent lithium-ion batteries, that would otherwise end up in landfills.
At Li-Cycle’s Spokes, the first stage of our business model, battery materials (spent batteries and battery manufacturing scrap) are safely recycled through a proprietary submerged shredding process (i.e., no thermal or pyro, so more environmentally friendly and safer) to produce black mass. Li-Cycle’s patented and environmentally friendly ‘Generation 3’ Spoke technology can directly process all forms of lithium-ion battery waste, including full electric vehicle (EV) battery packs, without the need for discharging and dismantling, which enhances safety and efficiency. The Spokes are designed to be zero wastewater discharge facilities and have zero combustion and direct greenhouse gas emissions.
At Li-Cycle’s Hub facilities, the second stage of our process, we will process black mass to produce critical battery materials, or the fundamental building blocks of batteries, including battery-grade lithium carbonate. Li-Cycle plans to use hydrometallurgy at its Hubs, which is a low-temperature and more environmentally friendly technology for processing black mass compared to traditional recycling methods.
With a recovery rate of up to 95%, how does your technology stand out in the battery recycling and materials recovery industry?
Li-Cycle is working to provide a sustainable and economic lithium-ion battery recycling solution by creating a secondary source of critical battery materials to help meet growing demand and ensure a more sustainable future for our planet.
Our Spoke and Hub Technologies™ include value-added differentiators, such as:
- Full pack, full charged shredding capabilities: Our Spokes can process full pack EV batteries without the need to dismantle or discharge.
- Efficient process: Our technology enables up to a 95% recovery rate to return critical materials back to the supply chain.
- Battery form agnostic: We are able to safely receive and recycle lithium-ion batteries and battery manufacturing scrap regardless of form factor and state of charge and condition. We are highly specialized in our ability to process damaged, defective or recalled batteries.
- High-quality, in demand products: Li-Cycle’s Hubs are expected to produce high-quality, critical battery materials, including battery-grade lithium carbonate.
How does your ability to process full EV battery packs without dismantling or discharging give you a competitive edge?
Li-Cycle’s ability to process full EV battery packs without discharging or dismantling allows us to be agile in a market that is rapidly growing and shows the advantages of localized battery supply chains. We are seeing more and more batteries that are larger and very difficult to dismantle due to their construction. By being able to process these full-pack batteries without the need for dismantling, we are offering our partners a key service – it’s more efficient, more safe and offers a sustainable ‘urban mining’ solution that repurposes critical minerals from end-of-life batteries.
By 2030, the supply of recycling materials is projected to increase by up to three times versus 2025 levels as more end-of-life battery feedstock becomes available. We are seeing an increasing supply of recycling materials and a demonstrated lack of post-processing capacity.
What challenges do you face when handling damaged, defective, or recalled lithium-ion batteries, and how does your process address them?
Through our patented and environmentally friendly recycling technology, Li-Cycle can directly process all forms of lithium-ion batteries, including full EV battery packs and damaged, defective and recalled (DDR) material, without the need for discharging, dismantling or using any thermal processes, enhancing safety and efficiency. By shredding batteries in submerged conditions, Li-Cycle’s proprietary process helps mitigate the risk of thermal events. Li-Cycle’s experience, expertise, facilities and technology to safely handle all types of battery materials, can help support a safer EV industry.
The Rochester Hub is expected to process 35,000 tonnes of black mass annually. What is the significance of this capacity for the battery supply chain?
There is a noted lack of post-processing recycling capacity, and our Rochester Hub is expected to help fill this critical need. The Rochester Hub can recover critical materials that are necessary for the lithium-ion battery supply chain that will support domestic energy independence for the U.S.
The Rochester Hub is expected to be North America’s first commercial hydrometallurgical resource recovery facility and a significant domestic source of recycled critical materials.
Once fully operational, Li-Cycle expects the Rochester Hub to produce up to approximately 8,250 tonnes of lithium carbonate, up to approximately 72,000 tonnes of MHP (mixed hydroxide precipitate) per year. MHP is an intermediate product that contains cobalt and nickel, key materials needed to produce lithium-ion batteries.
By introducing the recycled critical materials back into the lithium-ion battery supply chain, Li-Cycle closes the loop in a way that is both environmentally and economically sustainable and helps secure domestic energy independence.
Of note, we recently closed a $475 million loan facility from the U.S. Department of Energy (DOE), a key milestone as we look to develop the Rochester Hub facility. The closing of the loan is a strong vote of confidence in our patented recycling technology, as this is the first DOE loan to be finalized for a battery resource recovery facility.
Can you discuss the high-quality end products you produce, such as battery-grade lithium carbonate, and their importance for meeting industry demands?
At Li-Cycle’s Spokes, lithium-ion batteries of all formats and state of charge are processed through a mechanical “submerged shredding” process. This process breaks down the batteries to inert materials that minimize the risk of fire or explosion, and subsequently separates the resulting materials into two main product lines: black mass (battery materials) and mixed copper/aluminum.
As stated in our response to question 5, Li-Cycle believes that introducing the recycled critical materials back into the lithium-ion battery supply chain through an ‘urban mining’ approach, Li-Cycle closes the loop in a way that is both environmentally and economically sustainable and helps secure domestic energy independence.
The black mass produced at our Spokes would then be processed at the Hub which would then recover these critical battery materials, lessening the reliance on mining and its associated environmental impacts. It will also lessen the need to import these critical materials to strengthen domestic energy independence and bolstering national security.
What recent developments, like the $475 million loan from the U.S. Department of Energy, mean for your expansion and growth plans?
In 2024, Li-Cycle secured a $75 million strategic investment from Glencore and closed on an upsized $475 million loan from the U.S. DOE. This financing demonstrates Li-Cycle’s important role in the U.S. battery materials supply chain as a domestic supplier of recycled critical battery materials and speaks to the strong relationships we have with key industry partners.
As part of our growth plan, we are focused on securing a full funding package needed to restart construction at our flagship Rochester Hub project. The DOE loan is a critical milestone for this full funding package. In parallel with this work we are moving forward with plans that will optimize our Spoke operations, enabling us to build a self-sufficient and financially accretive Spoke business.
We continue to gain commercial traction while leveraging the capabilities of our Generation 3 Spokes. During the first nine months of 2024, our largest customer source of revenue was a U.S.-headquartered, vertically integrated EV and battery manufacturer with a substantial global EV market share. In Q3 2024, Li-Cycle expanded a recycling agreement with one of the largest EV OEMs in Europe; we now have recycling contracts with four of the largest EV OEMs on the continent.
What role does innovation play in overcoming the challenges associated with battery form factors and charge states during recycling?
Innovation plays an important role in meeting the challenges associates with battery form factors and charge states during recycling. Our technology is designed to be battery agnostic, and our submerged shredding process allow allows batteries to be recycled without being discharged, and without the need for thermal processes. For further information, please see our response to question 2.
How does Li-Cycle balance the demands of a fast-growing market with the need for environmentally sustainable practices?
Sustainability is foundational to our operations, an important part of our business model and a key element of our value proposition. Our process and patented Spoke & Hub Technologies are designed to be sustainable, and our environmentally friendly solutions offer an innovative and compelling alternative to existing mining practices and high temperature recycling.
Looking ahead, how do you see Li-Cycle influencing the global transition to clean energy and a circular battery economy?
As a leading lithium-ion battery resource recovery company, Li-Cycle is working to increase domestic supplies of battery-grade materials to support energy independence and national security. Not only does our recycling technology offer a sustainable alternative to mining, but it is also an environmentally friendly solution compared with other recycling processes. Our ‘urban mining’ approach provides an environmentally friendly closed-loop recycling solution, we create a secondary source of critical battery materials to help meet growing global demand and ensure a more sustainable future for our planet.
Comments are closed.